Injection molding is a process of transforming molten plastic into finished parts or products. These parts can range from a few ounces to hundreds or even thousands of pounds. They’re found in everyday hardware, computer parts and automobiles.
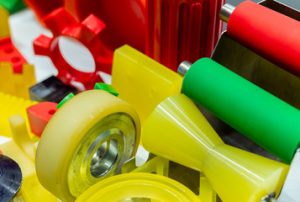
This is an efficient manufacturing method that uses very little material and produces very few defects. The molds are usually made of steel or aluminum and precision-machined. Read on American Plastic Molds for more details.
Custom plastic molding is a great way to bring unique products to life. It is also very economical and environmentally friendly. It is used for products that require intricate shapes, curves, or contours. It is also used to add features like logos and slots for metal inserts. It is important to choose a custom plastic mold manufacturer that has the experience and expertise to produce high-quality parts. ICOMold by Fathom is one such company, with decades of experience and a wide range of capabilities.
The process of custom plastic molding involves creating a digital design and analyzing whether it is viable in the market. It also includes a series of rapid prototyping sessions. Once the product meets the necessary specifications, it is then molded. This is a highly customizable process that can produce precise shapes and sizes for a number of different applications.
There are many different types of plastic injection molding, including single-cavity, multi-cavity, and family molds. These vary in complexity and cost, based on the product and the number of units that are required. It is important to consider the type of plastic or resin that will be used, as this will have an impact on the final product.
Plastic injection molds are often made using a process called extrusion, which uses hot melted plastic to create long-shaped parts. The liquid plastic is pressed through a die that is custom made for the desired outcome, much like pressing dough through a cookie cutter to make shaped cookies.
Plastic injection molds are used in a variety of industries, from medical equipment to car manufacturing. They are highly accurate and can be produced quickly, making them a popular choice for production. The ability to customize these tools to fit a customer’s specific needs is another reason why they are so popular. This customization ensures that the plastic injection mold will be a good match for the final product. In addition, it helps reduce the risk of defects and increases overall productivity. The process of creating a plastic injection mold prototype is quick and easy, and it is a great way to test the design before starting production.
Efficiency
The quality of plastic molds has a direct impact on the final product. This is why it’s important to pay close attention to the details and precision of the design before beginning production. This will help ensure the efficiency and longevity of the molds. In addition, it will also reduce the risk of mechanical problems that can result in costly production halts.
There are many ways to improve the efficiency of your company’s plastic injection molding processes. For example, investing in new technology can significantly reduce the time it takes to produce your products. This includes ERP software, simulation programs, CMM machines, and robotics. These technologies can also increase employee motivation and overall productivity. However, it is important to remember that implementing these new technologies will require a financial investment.
Injection molding is a high-temperature process that involves liquid raw material being poured into a heated mould. It is then compressed together and cooled to give the product its shape. The end product is then trimmed and removed from the mould. This is a popular method for manufacturing a wide range of plastic products including automotive parts, surgical equipment, and more.
While this technique is highly efficient, there are some things to keep in mind when selecting a plastic mould manufacturer. For one, it’s essential to find a company that offers competitive pricing and high-quality work. It’s also important to ensure that the company has a high level of technical expertise, especially when it comes to designing and building complex plastic products.
Moreover, the quality of the plastic moulds and injection molding machine plays a crucial role in the production of quality plastic parts. For example, the clamping force needs to be optimized to avoid flash-a defect that occurs when excess plastic leaks out of the mold. Similarly, the injection pressure should be optimized to ensure that the molten plastic fills the mold cavity evenly. In addition, the cooling time should be minimized without compromising part quality.
In addition, the way a plastic mold is stored when it’s not being used can greatly affect its durability. For instance, a recent study showed that climate-controlled storage increased mold life by 20% compared to standard storage. It is also important to ensure that your employees have the right tools and training to handle the machine properly.
Environmentally friendly
Plastic molding is a fast, cost-effective process that has numerous environmental benefits. Using recycled plastics, utilizing energy-efficient machines and optimizing the production process all contribute to sustainable practices in plastic injection molding. Additionally, the long lifespan of molds reduces the need for constant replacements, further contributing to sustainability.
As the world moves towards greater environmental responsibility, plastic molding companies are leading the charge with eco-friendly practices that can help save both money and the environment. Incorporating recycled plastics into products helps reduce the need for new materials, and bio-based plastics can be used to create more environmentally responsible alternatives to traditional fossil fuel-based plastics. In addition, the use of advanced mold designs and conformal cooling can significantly reduce the amount of waste produced during production.
Another green practice is using renewable energy sources to power injection molding machines, which can further cut down on carbon emissions. Finally, reducing transportation distances and streamlining the supply chain can also help reduce emissions. For unavoidable emissions, companies can also participate in carbon offset programs to neutralize their impact.
Plastics are a versatile and durable material that can be used for many applications. When they are discarded, however, they can have a negative impact on the environment. Plastics can damage ecosystems by accumulating in landfills, polluting waterways and entering the food chain. When plastics are not properly disposed of, they can also cause harm to wildlife and animals.
The good news is that sustainable practices are becoming the norm in plastic injection molding. From using eco-friendly plastics to implementing energy efficiency, these trends are transforming the industry into a more environmentally responsible sector.
Injection molding is a versatile manufacturing technique that can be used to create a variety of different products. It is often used in conjunction with other manufacturing methods, including blow molding and extrusion. It is particularly well suited for hollow parts, such as car parts, bins and storage tanks. It is also ideal for large, hollow components that need to be molded in one piece. It is important to understand the limitations of injection molding, however. Some common failure modes include wear loss, local plastic deformation and fracture.
Economical
Plastic injection molding is an efficient production method with minimal scrap waste. It is also environmentally friendly because it uses less energy than other manufacturing methods. Its advantages include its ability to create parts with complex shapes and features, as well as the option of reusing scrap plastic for future projects. Additionally, it is an ideal manufacturing process for large-scale production runs of varying quantities.
The use of various materials in injection molding results in a wide range of final products, from food containers to automotive parts and medical devices. Each material has a different price point and cost associated with it, so it is important to understand how these factors affect the overall cost of production. This knowledge will enable manufacturers to optimize production processes and make informed decisions about design and material selection.
Injection molding is a versatile, high-volume production technique that offers significant economic benefits. Its efficient production process reduces costs by lowering labor and energy consumption, as well as reducing the number of defects. The resulting parts are highly durable and can be used in a variety of applications. Injection molding is also an environmentally-friendly method of manufacturing, as it produces very little waste plastic and allows the unused material to be reused.
A thorough mold cost analysis helps companies identify areas where expenses may exceed initial estimates, allowing them to address these issues proactively and minimize budget overruns. This approach also fosters a culture of continuous improvement, encouraging businesses to seek innovative solutions and pursue efficiencies without sacrificing quality.
Bringing injection molding production back to the United States can help rebuild the country’s industrial base and create good-paying jobs in the process. Moreover, it can reduce transportation and shipping costs, as well as support innovation by providing local engineers with the resources they need to develop innovative product solutions. Additionally, building molds closer to the production facilities enables better oversight and quality control, minimizing the need for expensive rework and repairs.