A chimney in poor repair is vulnerable to damage from harsh winter weather. Watch for cracks, crumbling bricks, and deteriorating mortar joints.
Even small issues should be addressed immediately. Failure to do so can lead to a leaning chimney, which compromises the structure and exposes your home to carbon monoxide poisoning. Contact Chimney Repair Baltimore now!
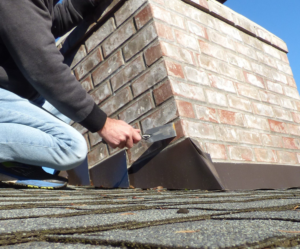
Heavy rains can cause your chimney to leak, especially if the flashing and chimney crown are in need of repair. Leaking chimneys can be very destructive and dangerous for the fires you light inside your home. If you notice a damp spot on your ceiling or walls, have a professional inspect the fireplace and chimney for water damage. A professional can use a variety of repair techniques to address the issue, depending on the severity of the damage and its location within the chimney structure.
Chimney gaps are a common cause of water leaks and must be repaired immediately to prevent further damage to the brick structure. Cracks and gaps in the mortar joints can let in rainwater, which may also freeze when it gets cold. This will make the cracks expand and can further weaken the mortar structure of your chimney.
Another sign of a chimney problem is a damper that is not working properly. The damper is a necessary part of your chimney that regulates the flow of air through the flue. If you notice a damper that is not opening or closing properly, contact your local chimney technician. They can inspect the condition of your damper and determine if it is in need of repair or replacement.
Chimney flashing is a metal seal that wraps the area where your chimney meets the roof of your house. It is designed to prevent rain water and snow melt from seeping into your fireplace. A damaged or missing chimney flashing can allow water into the chimney, resulting in costly water damage to the attic and walls of your home. If you suspect your chimney flashing is in need of repair, contact a chimney and roofing expert as soon as possible to avoid extensive water damage to your home.
The masonry materials of your chimney are naturally porous, making them susceptible to water penetration. Water damage to a chimney is exacerbated when it becomes freezing, as the water expands and erodes the bricks and mortar of the structure. Chimneys built of clay tiles, in particular, are prone to this type of damage. If you notice signs of water damage, including efflorescence, spalling brick, and deteriorating mortar joints, call for a chimney inspection. Your chimney expert may recommend a repair service like tuckpointing or rebuilding to restore the structural integrity of your chimney.
Cracked Mortar Joints
Mortar joints between bricks are a key component of the durability and longevity of brick walls, chimneys and other structures. These joints absorb the stress of wall movement, foundation settlement and exposure to the elements. They also provide a buffer between bricks, helping to prevent moisture from entering and causing damage. Cracked mortar joints should be repaired as soon as possible to avoid serious problems in the future, including water leaks, mold growth and other structural issues.
Masonry repair experts use a process called pointing (also known as repointing or tuckpointing) to restore and preserve mortar joints that have eroded due to age, weather, temperature changes and other factors. This process involves mixing a new batch of mortar and applying it to the mortar joints. In most cases, the color and texture of the new mortar should closely match the existing mortar in the joint.
When repairing cracked mortar joints, it is important to first clean the work area thoroughly and remove any loose or crumbling brick. Then, wearing safety goggles, a cold chisel and hammer can be used to cut at least 1/2 inch down into the old mortar, flushing the joint clean and creating a solid base for the new fill. Once the damaged mortar is removed, the work area should be cleaned again using a masonry brush to make sure there is a clean surface for the new mortar to bond.
Once the work area is prepped, a mortar mix that closely matches the existing can be mixed according to manufacturer instructions and loaded into a tuck-pointing trowel. The new mortar should be pushed into the joint and sculpted to match the existing brick, removing any excess as it hardens. To ensure the new mortar dries correctly, it may be necessary to wet down the brick and joints with a hose a few times per day for two or three days.
For smaller cosmetic repairs, a caulking gun and sanded acrylic mortar repair caulk can be used to apply a bead of caulking into the joint. The sanded caulk offers the texture and appearance of mortar, making it an option for homeowners who are hesitant to attempt a mortar mixing project.
Efflorescence
Efflorescence is the white, chalky substance that accumulates on brick chimneys, as well as other masonry structures. It’s a common sight and is often mistaken for dirt or weathering, but it’s actually a tell-tale sign of moisture problems within your chimney structure.
Essentially, efflorescence is the result of water seeping into a chimney’s masonry and dissolving the soluble salt particles naturally present in the brick, stone or concrete. As the water evaporates, it leaves a residue of salt on the exterior of your chimney that shows up as a white or sometimes brownish crystalline deposit.
It’s possible to prevent the formation of efflorescence by using building materials that don’t contain high amounts of soluble salts during construction, ensuring that your chimney is properly sealed, and providing adequate drainage away from your chimney. Additionally, you can reduce the likelihood of efflorescence developing by providing a proper chimney liner and making sure there is no cracking or leakage in your roof’s flashing.
If you notice the unmistakable white stains of efflorescence on your chimney, you should contact a professional chimney mason for an inspection right away. They’ll thoroughly examine the area, looking for cracked brick, mortar joints, missing mortar, damaged flashing and other signs of excessive water penetration. They’ll also recommend a chimney waterproofing sealant to keep the stains from returning in the future and protect your chimney against more extensive damage.
Although some efflorescence is normal and harmless, it can indicate a serious problem that needs to be addressed immediately. It may be caused by rainwater soaking into the masonry, or it could be that your flue liner is cracked and leaking hot gases from the fireplace down into cold brick, where they condense and cause the masonry to deteriorate quickly.
While you can clean some forms of efflorescence by washing the crystalline deposits with water or by applying an acidic solution, it’s best to leave this type of chimney repair to a certified mason. Attempting to power wash or sandblast off these deposits can be dangerous for you and your chimney, and it won’t stop the white stains from returning.
Degradation
Chimneys look strong, and so it’s easy to forget that they need maintenance just as the rest of our homes do. Rain can damage the masonry, or mortar joints, causing it to deteriorate. Depending on the extent of the damage, this can be very dangerous as it reduces the strength and fire proofness of your chimney structure. One way to spot degradation is by looking for bits of masonry on the ground near your fireplace. Another is to notice the presence of moss on or inside your chimney. These signs indicate that your chimney is deteriorating.
Chimney deterioration is most commonly caused by water damage, but it can also be due to other factors. For example, if your chimney liner is not properly installed, it may not prevent condensation that leads to acidic creosote buildup. This can cause drafting issues, and can lead to chimney explosions.
Having your chimney regularly inspected by a professional is the best way to catch any problems that need to be repaired, including degradation. Degradation is a natural process, but it can accelerate dramatically if your chimney is not protected from water damage.
Mortar joints are a common place for moisture to enter your chimney, but the bricks themselves can also deteriorate. This is known as spalling, and it’s an extremely serious problem that requires immediate attention. It causes the bricks to fall apart, which exposes your chimney to further damage and a significant safety hazard.
Another issue that can result from water entering your chimney is rusting. If your chimney has a metal flue liner, it will likely be constructed from aluminum or steel. These metals are not prone to corrosion, but your flue liner can still rust and lose its ability to convey combustible gasses safely out of your home.
If you’re concerned about the state of your chimney, it’s important to understand the clear warning signs that indicate a need for repair. It’s important to inspect your chimney from all angles, using binoculars to get a closer look at hard-to-see areas. If you see any cracks or deterioration, call a chimney specialist right away to schedule a repair appointment.